Ophthalmology:
Detection and measurement
of lens defects
Specialist in the inspection
of implantable lenses (IOLs) and contact lenses (CLs)
V-OPTICS is a unique partner on the way to achieve «zero defects».
Our QualiLENS® solution, dedicated to the qualification of IOLs and contact lenses makes it possible with a single piece of equipment to address:
- Dimensional inspection (diameter, haptics (IOLs))
- Engraving reading (“letters and numbers”, optical axis location)
- Automatic detection of defectd (chips, scratches, lathe and machining defects, etc.)
QualiLENS® systems are by nature customisable. Thanks to their multiple functionalities, reliability, speed and ease of use, many customers around the world rely on V-OPTICS to improve their processes.
To adapt to different production processes, two versions are available:
- QualiLENS® 150 for «BATCH» production (per batch / tray).
- QualiLENS® 100 for «ONE PIECE FLOW» production.
To meet the needs of the most demanding customers, in addition to the “product qualification and measurement” aspect, we have made QualiLENS® easy to use, maintain and ready for automation:
The V-OPTICS measurement technology does not require precise positioning of the lens for measurement. |
A lens can be identified automatically at the time of inspection, thanks to code and engraving reading capabilities. |
For BATCH processes, «smart tray management» makes it possible to track batches of lenses - on a connected sorting station, right through to the “container” removal operation. |
The interface with production management systems allows, real-time data exchange and remote control of the equipment, via digital signals and the computer network. |
QualiLENS® is suitable for use in cleanrooms and easy to operate thanks to “touch-sensitive” interfaces. |
The QualiLENS® is specially designed to make production automation easy, and to control quality by ensuring efficient traceability.
QualiLENS® 100
Dedicated to the automated inspection of single contact lenses, the QualiLENS® 100 is suitable for use at an opertor workstation.
As part of an automated/robotic line, the QualiLENS® 100 is fully adapted to fit into a “ONE PIECE FLOW” type production flow.
There are three stages to lens inspection:
1
The lens is loaded into the “sample holder” for measurement in different ways, depending on whether the measurement is taken in an aqueous medium or in air.
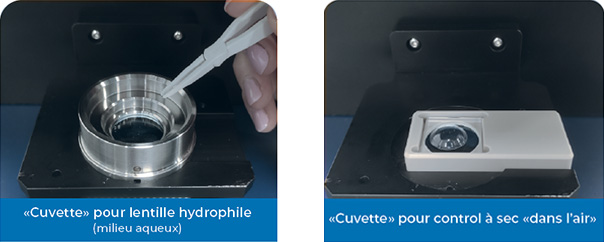
2
The operator triggers the inspection process.
It takes just a few seconds to obtain the results of the various measurements, reports, and data archiving.
3
The operator can remove the lens from the system and pack it for the next stage of production.
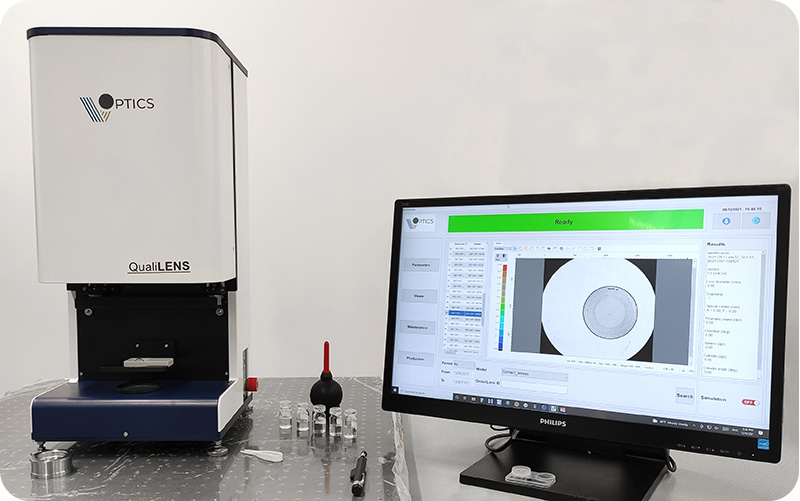
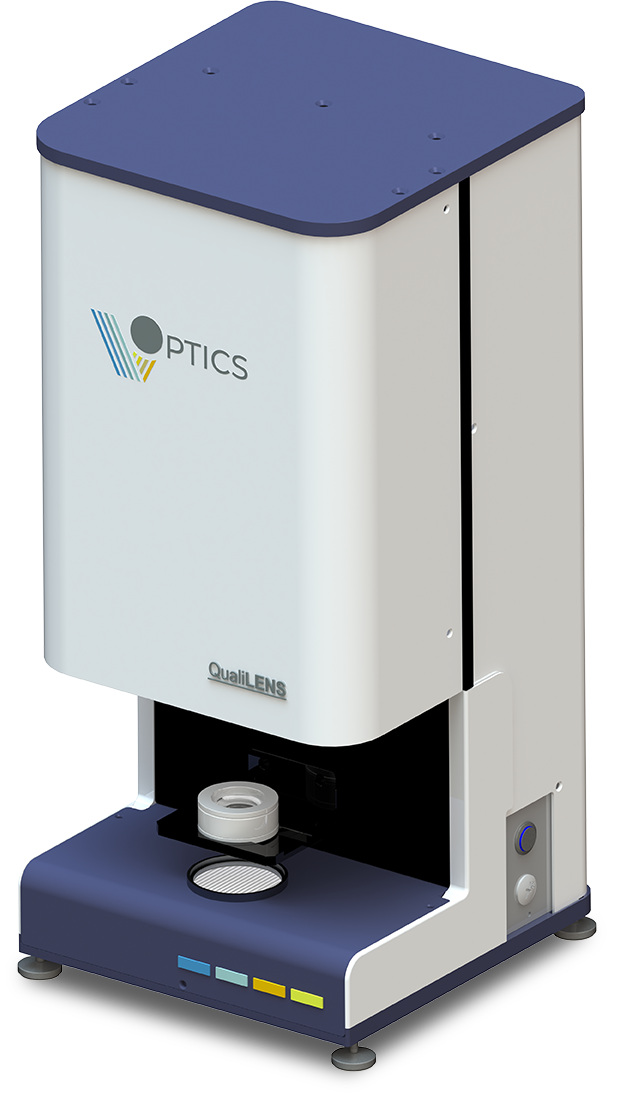
For integration into automated lines, the QualiLENS® 100 is available in a specific version, more suitable for robotic loading.
The QualiLENS® 100 is delivered with all the sensors, software and data processing electronics required for its operation.
V-Optics also handles commissioning and the essential settings, in collaboration with the customer. The customer is trained by our teams to be fully autonomous in the use and adjustment of the inspection parameters.
QualiLENS® 150
The QualiLENS® 150 is the ideal solution for fully automated “BATCH” production inspection.
There are three stages in the inspection of a batch:
1
The contact lenses in a batch are placed in “test case” or “trays” specially designed for treatment in an aqueous or dry (air) environment, depending on the case. Each contact lens is placed in an individual cavity.
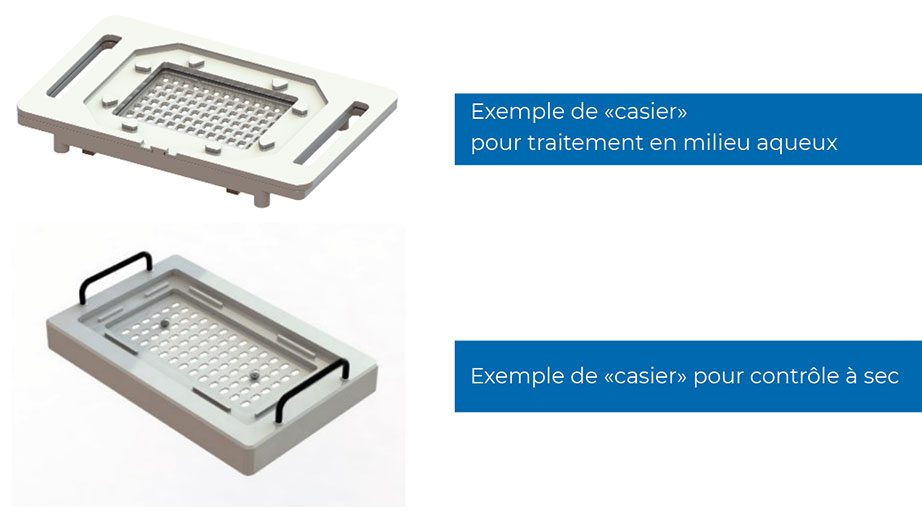
2
The «tray» is positioned in the QualiLENS® 150. The test cycle begins.
3
The "tray" is remove from QualiLENS 150 and placed on a special tool called “connected sorting table». A backlighting system illuminates each cavity containing a lens, allowing the operator to process it according to the colour code (green = compliant, red = rejected, orange = operator decision possible).
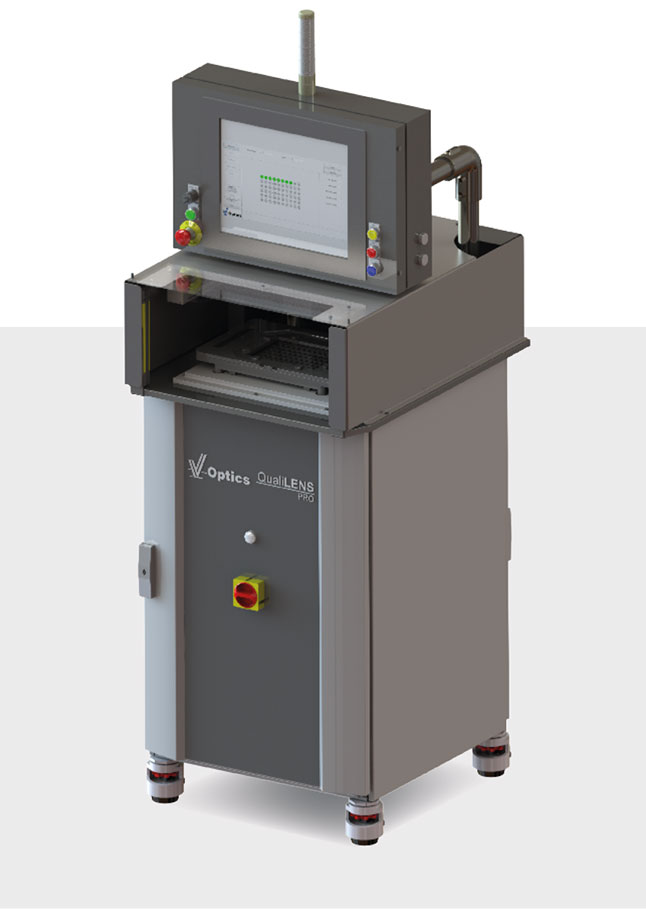
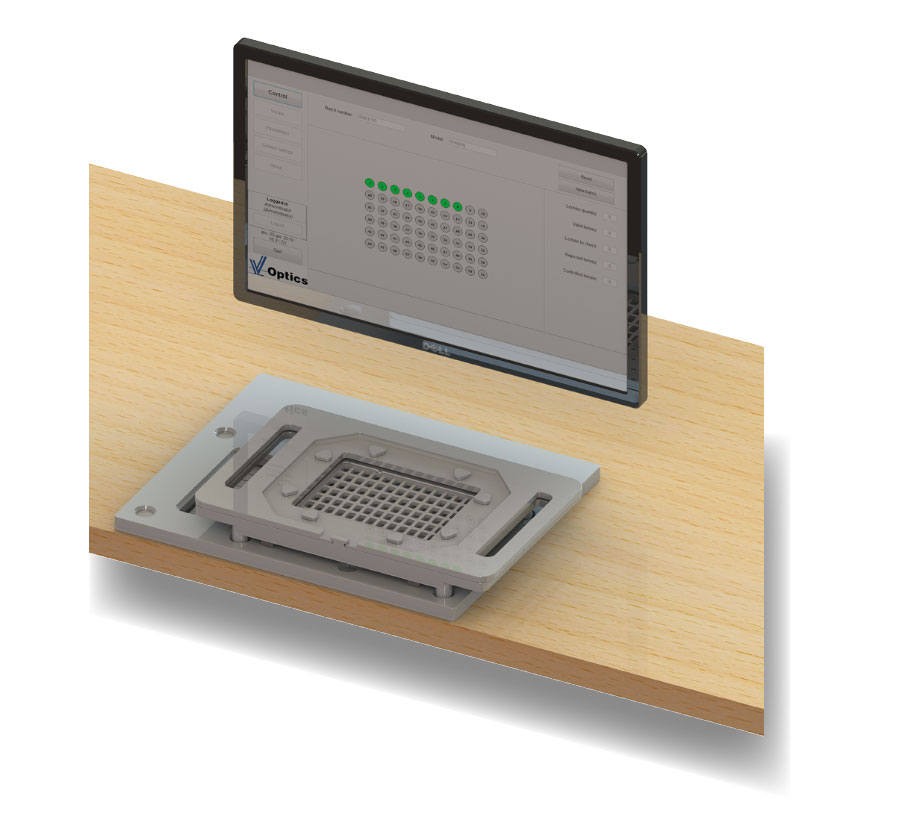
The filling of trays and the inspection and removal of lenses after measurement can be carried out asynchronously. To track batches of lenses in such a process, the “trays” are equipped with an intelligent tracking system, based on RFID technology, compatible with the cleaning and sterilisation processes.
Actually, when the lenses are placed in a test case, a digital link is established between the batch and the test case. This information is then available in the QualiLENS® 150 or on the sorting table. The results of a batch of lenses are then displayed without any user action, as soon as a test case is placed in the QualiLENS® or on the sorting table.
Example of implementation and use:
- 1 The lenses are cleaned and loaded into the trays (1 batch per tray).
- 2 A tray is loaded into the QualiLENS® 150.
- 3 The tray is identified, along with the information of the batch of lenses in it.
- 4 The QualiLENS® 150 measures all the lenses.
- 5 At the end of the cycle a light and/or sound signal is generated.
- 6 The tray is unloaded from the QualiLENS®, which is again available to receive the next tray.
- 7 The operator places a tray previously inspected by the QualiLENS® on the “sorting station”. The station automatically displays information about the tray’s contents. The backlighting of each cavity shows the operator whether a lens is compliant or not.
- 8 Once the tray has been emptied, the operator tells the system that the batch has been processed.
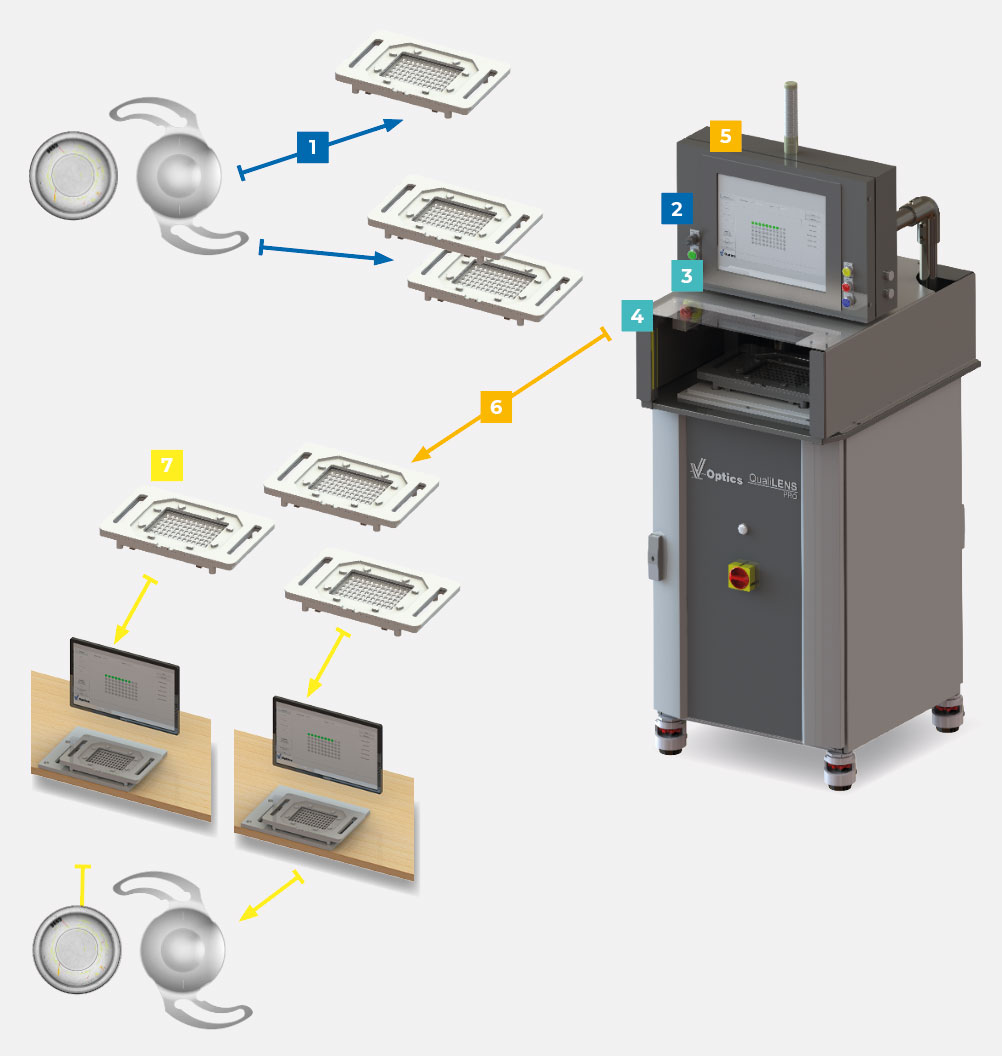
Several sorting tables can be connected simultaneously to a QualiLENS® 150, allowing the unloading and final packaging of lenses to be combined in a single workstation.
Simplicity, user safety and traceability were the guiding principles in the development of the QualiLENS® 150.
More information about QualiLENS®
01 Main functions and measurement of optical characteristics
Products for QualiLENS® 100 and 150
- Inspection of rigid and flexible contact lenses
- Inspection of hydrophilic and hydrophobic implantable lenses (IOLs)
- Inspection of simple, toric and multifocal lenses
- Measurement in air (dry) or «in situ» (aqueous environmemnt)
Main features available on QualiLENS® 100 and 150
- Intuitive, easy-to-use software
- Secure settings, secure user access
- Detailed measurements results available for archiving and traceability
- Measurement results available for production management software
- Production order data extraction for machine inspection
- Inspection reports available per lens, and per batch
- Automatic monitoring of the system and tooling (sample holders, test cases)
- (150 only) Tray management and tracking by using RFID technology
- (150 only) Connection with «filling station» and «sorting station»
- Automatic qualification of whether or not the contact lens is compliant
- Semi-automatic qualification possible with operator intervention
02 Measurements and defect detection
Dimensions :
- Diameter of the lens (CL)
- Inspection of haptics and design (IOLs)
- Inspection of holes
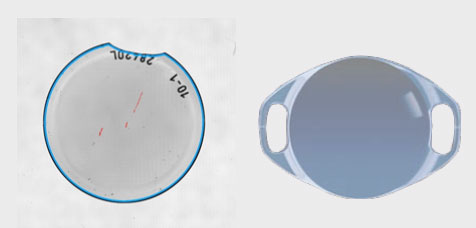
Laser engraving/ codes:
- Engravings reading and quality control
- Depending on the code: verification and inspection of the possible management
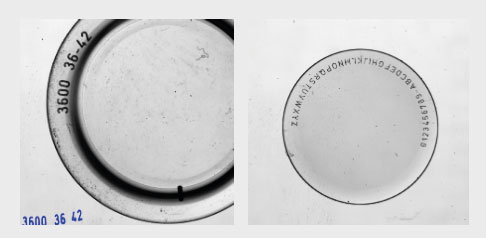
Defect detection:
Automatic (or semi-automatic) detection of defects such as:
- Chips
- Decentering
- Handling marks
- Inclusions
- Center point
- Lathe marks
- Milling marks
- Tear out of material
- Edge defects
- Scratches
- Haptic damages
- Others on request
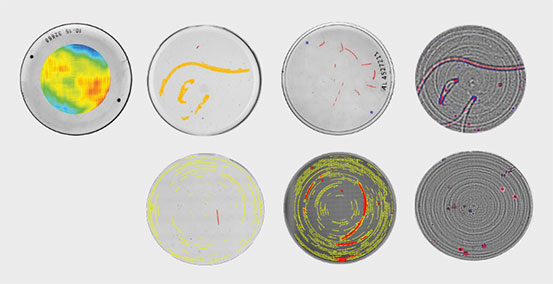
Examples taken from the QualiLENS® defect database:
03 Lenses quality control principle
The user can define contact lens inspection criteria according to their needs (by type of contact lens, customer, reference, etc.).
These criteria can be defined individually, according to 3 areas whose dimensions are freely definable by the user.
1AREA 1 (optical centre) 2 AREA 2 (peripheral area) 3 AREA 3 (edge/external area)
The inspection criteria can be modified for the different areas above via a dedicated interface. The simulator allows you to see, in real time, the effect of a change in criteria on data from archived lenses.
This makes it possible to develop offline settings, then test and validate them on data from production before integrating them.