Situation
Our customer is a leading manufacturer of implantable ophthalmic lenses.
These lenses are designed to offer patients enhanced visual independence, reducing or even eliminating the need for glasses or contact lenses.
The company operates in the field of ophthalmic surgery where quality, traceability and even the slightest defect are crucial concerns.
Challenge
This manufacturer initiated a major modernization of th e production process, affecting both manufacturing machinery and quality control.
At the heart of this transition, final cosmetic inspection represents a major challenge. This control is carried out manually, a method perceived as outdated and highly subjective.
Currently operators inspect every single lens with naked eye s through binoculars, seeking defects related to lathe marks, scratches, chipped edges, inclusions, and more.
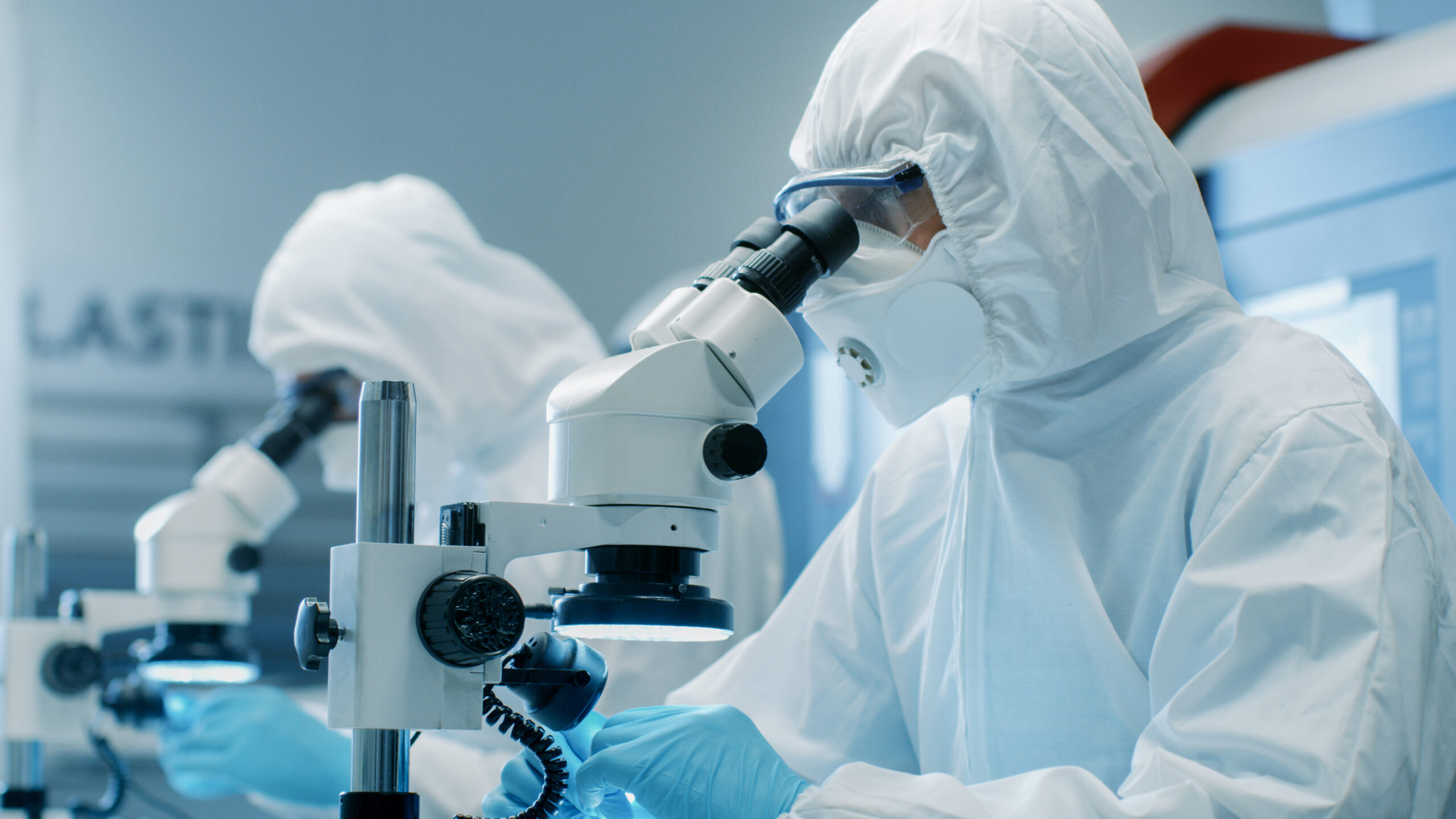
The goal is to automate the production line as much as possible .
Solution
After discovering our QualiLENS® 100, they sent us samples of lenses with representative defects for a first assessment of the device capabilities.
The aim was to automatically detect and classify defects on batches of lenses.
Tests with the QualiLENS® 100 proved to be very conclusive, enabling defects to be detected and labelled accurately:
“When I attended the presentation of the results, I was blown away by the precision and repeatability.”
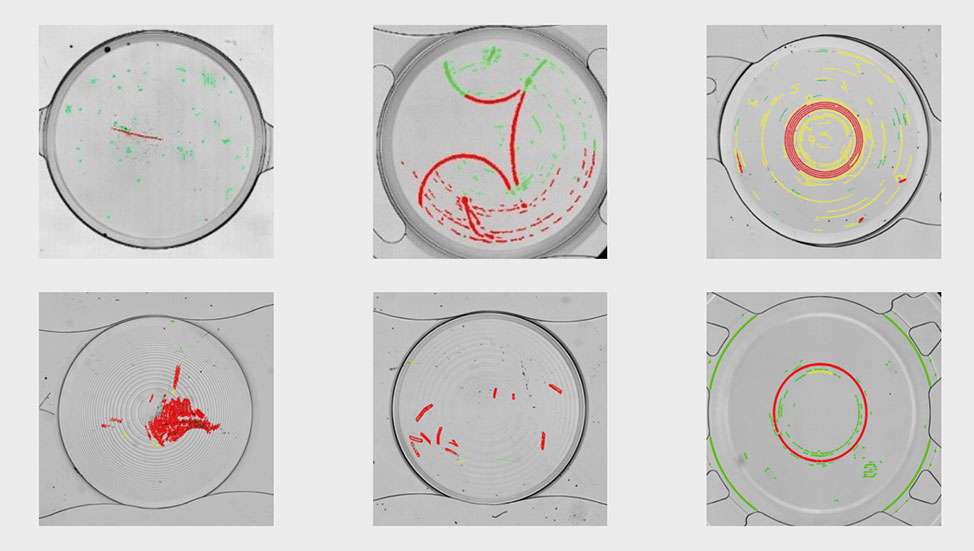
Very satisfied with the initial outcomes, they decided to purchase one machine.
To make this ambitious project a success and meet their high expectations and regulatory requirements, it was necessary to adopt a collaborative approach.
Our customer allocated proper internal resources and a genuine teamwork started with our team of experts. Together we optimized the algorithms and developed the methodology necessary to implement the QualiLENS® 100 into their production line.
It has been an iterative process , featuring numerous testing campaigns aimed at improving the machine’s performance and fine tuning the algorithms to better detect defects inherent to their production.
We also implemented specific developments to adjust elements such as the user interface’s ergonomics and the format of the output data.
Outcome
Our customer validated the solution technically for the production and approved an investment plan to equip all their production lines in the coming years.
Considering the medical device nature of their products, regulatory procedures are in the final stages of approval with regulatory authorities. As soon as the green light is given, deployment will start on their production lines.
They already see 3 major benefits:
- Dramatic improvement of the objectivity and consistency in inspection
- Traceability thanks to the capacity of the system to store images and
reports totally inexistant in the case of visual control - Significant savings in term of resources
The result is a wow effect.
They expressed their enthusiasm many times , by highlighting the significant leap forward in their lens inspection process.
“We’ve been manufacturing lenses for 50 years and inspected them the same way, but now we’re entering a new era. We get a 21st century inspection equipment.”
Optical Engineer
Leading manufacturer of implantable lenses