Faurecia & V-OPTICS
For more than 100 years, Faurecia has been one of the world’s leading automotive suppliers. The company is present in more than 35 countries around the world with 266 industrial sites, 39 R&D centers, and 114,000 employs.
At the end of 2019, as part of a research project, the Interior Systems division was looking for a solution that would allow Faurecia to ensure the durability of its paintings. Ms. Mathilde DELORY, a development engineer, discovered the deflectometry on the V-OPTICS website. “Deflectometry was new to me at the time and I was pleasantly surprised,” she explains.
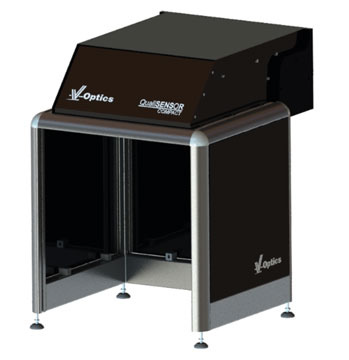
The sensitivity of the human eye scanning a surface and its reflections is difficult to digitize. This problem, with significant industrial consequences, is particularly complicated to implement in a classic industrial vision because it requires both robustness and repeatability. Not all of the surface characterization systems tested by Faurecia have enabled it to perform such a rapid (a few seconds is enough) and complete assessment of surfaces.
Initially, Faurecia invested in 2020 in a QualiSENSOR Compact system intended for an R&D project. The sensor will soon be installed on a production site for quality control.
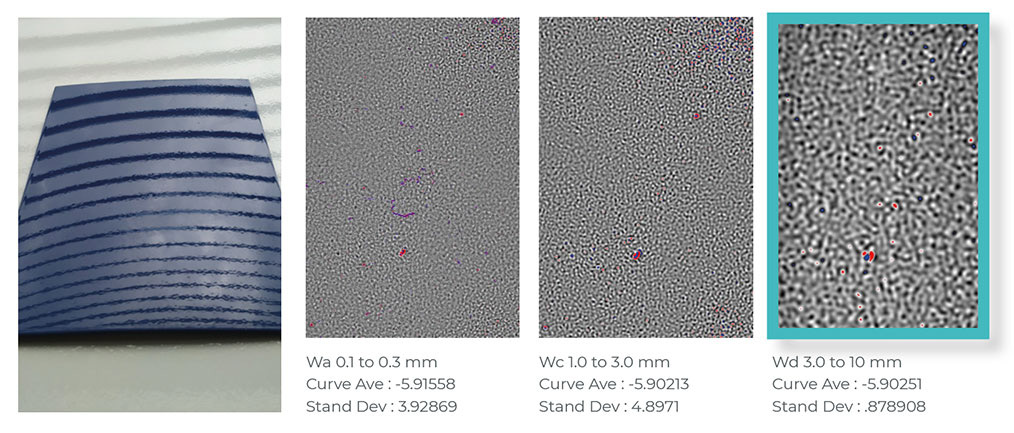
QualiSENSOR is used daily and Faurecia is very satisfied with the results it provides.
“3 μm resolution! It’s amazing to get so much information with such precision over a large area in 10 seconds. This is therefore the best surface/resolution compromise for our application. The technology is really complementary, ”says Ms. DELORY.
Today, several Faurecia departments are sending parts to Lyon to assess injection defects (indentations, hollows, bumps). The results are also very satisfactory and it is possible that Faurecia will use this sensor for these issues specific to plastic injection, before painting.
In addition, Faurecia congratulates V-OPTICS from a relationship and sales point of view. The team listens to the client issues and works to resolve complications or difficulties such as the design of an ATEX version of the sensor.
“I appreciated that you took the time to spend 2 weeks after installation to see if everything was okay and to advise me on the flatness measurement at the same time. “Underlines Ms. DELORY, the main user of the installation, who also specifies that” the system is easy to use“
Listening to customers is the key to the development of new business standards. V-OPTICS attaches particular importance to understanding its customers’ issues through the mission of application engineers who are closest to the field.
This success story marks the beginning of a relationship of trust that has only just begun.